Unlocking Precision: The Importance of Calibration Services
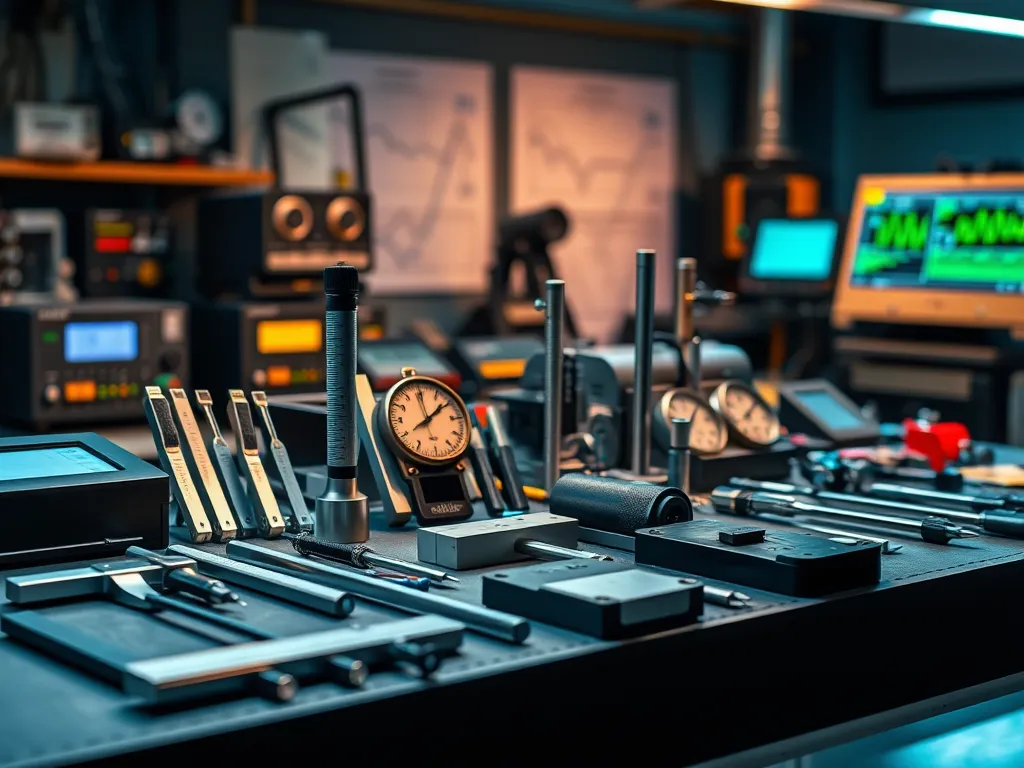
Calibration Services in Precision Industries
Calibration Services in Precision Industries play a vital role in ensuring the precision and reliability of measurements across various sectors. These services are designed to calibrate instruments and equipment, guaranteeing they provide accurate data and operate efficiently. In an industry where errors can lead to significant financial losses or safety hazards, the importance of regular calibration cannot be overstated.
In Precision Industries, where products are often manufactured to exact specifications, Calibration Services in Precision Industries ensure that tools and systems are functioning correctly. Regular calibration helps maintain the integrity of measurements essential in product development, testing, and production processes. By regularly calibrating measuring instruments, industries can maintain a higher level of quality assurance, resulting in improved product reliability and customer satisfaction.
The significance of Calibration Services in Precision Industries is evident in various key sectors, including aerospace, medical devices, automotive, and electronics. These industries rely extensively on precise measurements for performance, safety, and regulatory compliance. For instance, in the medical field, it's crucial that equipment like blood analyzers and imaging devices provide accurate readings, as any discrepancies could lead to incorrect diagnoses or treatments.
Moreover, Calibration Services in Precision Industries are not just limited to the initial setup of equipment but also involve regular maintenance and periodic checks to ensure ongoing accuracy. Depending on the equipment's usage and environmental conditions, calibration frequency may vary. This proactive approach to measurement accuracy helps mitigate risks associated with faulty readings and machinery malfunction.
In today's precision-driven industries, relying on expert Calibration Services is essential to ensure equipment accuracy and reliability.
In conclusion, Calibration Services in Precision Industries are essential for achieving optimal performance and reliability in a highly competitive market. By prioritizing calibration, companies can enhance operational efficiency, maintain product quality, and adhere legally to safety standards. These services not only support compliance but also reinforce consumer trust in the industries they serve.
Understanding Calibration Services
Calibration services refer to the set of procedures undertaken to evaluate and adjust the accuracy of measuring instruments and devices. The primary purpose of these services is to ensure that measurement instruments are providing accurate results according to predetermined standards. This process involves comparing the output of a measuring device against a known standard and making necessary adjustments to align the performance of the device with that standard.
Accurate measurements are critical in precision industries as they directly impact product quality, safety, and performance. Calibration ensures measurement accuracy by identifying any discrepancies between the instrument's actual output and the standard's expected output. Through systematic calibration, industries can minimize errors that might arise due to equipment malfunction, drift, or environmental influences.
Key industries that heavily rely on calibration services include aerospace, pharmaceuticals, telecommunications, automotive manufacturing, and food production. For these industries, even minor inaccuracies can lead to significant safety risks or compliance issues. As such, maintaining a rigorous calibration regime is essential to meet industry standards and regulatory requirements.
Benefits of Calibration in Precision Industries
One of the primary benefits of Calibration Services in Precision Industries is the improved accuracy and reliability of measurements. Regular calibration helps in maintaining devices and instruments, ensuring they deliver precise outcomes that industries can rely on. This accuracy leads to fewer product defects, reduced rework costs, and increased customer confidence.
Additionally, Calibration Services ensure regulatory compliance and adherence to industry standards. Many sectors, especially those governed by strict safety regulations, must demonstrate that their measuring instruments are regularly calibrated to meet compliance. This not only prevents legal and financial penalties but also enhances the credibility of the company in the marketplace.
Cost-effectiveness and resource optimization are further advantages of investing in Calibration Services. By accurately calibrating equipment, industries can extend the lifespan of instruments and avoid unnecessary replacements. Furthermore, reliable measurements reduce production waste and improve efficiency, leading to significant cost savings in the long run.
Calibration Standards and Practices
Calibration standards are established guidelines that dictate the process of calibrating various types of measuring instruments. These standards, often set by international organizations, ensure consistency and reliability across industries. Understanding these standards is crucial for calibration service providers to maintain quality and precision in their practices.
Best practices for effective calibration include maintaining accurate records, utilizing certified reference materials, and employing qualified personnel for calibration procedures. These practices help in tracking calibration data over time and provide a basis for ongoing quality assurance in measurement processes. Regular training and updates on best practices for calibration can also enhance the skill set of calibration technicians.
The role of accredited calibration laboratories is pivotal in adhering to calibration standards. These labs are equipped with highly advanced measurement instruments and operated by skilled technicians. Accreditation from recognized bodies ensures that the calibration services provided are of high quality and meet international standards, thereby enhancing the credibility of the calibration process.
Technological Advancements in Calibration
Emerging technologies in calibration equipment have significantly enhanced the precision and speed of calibration processes. Advanced tools such as laser-based systems, digital measuring devices, and automated calibration systems reduce the human error margin and increase accuracy. These technologies also enable real-time monitoring and adjustments, making the calibration process more efficient.
Software solutions for calibration management have also transformed the industry. These software programs help track calibration schedules, maintain records, and generate compliance reports. By automating these processes, industries can ensure that their calibration activities are timely and well-documented, easing the regulatory compliance burden.
Trends shaping the future of calibration services include the integration of artificial intelligence and the Internet of Things. These innovations are expected to enhance predictive maintenance capabilities in calibration, where devices can self-monitor and notify users when calibration is needed, thus further minimizing downtime and improving operational efficiency.
Challenges in Calibration Services
Common challenges faced in calibration processes include the variability of environmental conditions, equipment drift over time, and the complexity of calibration procedures. Such factors can complicate the calibration process and hinder the ability to achieve accurate measurements consistently. Industry professionals must be aware of these challenges to implement effective solutions.
Human error remains a significant factor affecting calibration outcomes. Mistakes made during the calibration process—such as recording data incorrectly or misinterpreting readings—can lead to inaccurate results. Continued training and the implementation of standardized protocols can help reduce the incidence of human error in calibration services.
Maintaining calibration integrity in industrial settings commonly faces hurdles, including operating under varying environmental conditions and the wear and tear of equipment. Regular assessments are essential to address these challenges and ensure that measuring instruments provide dependable readings in all circumstances.